Uma visão de Profibus, desde a instalação até a configuração básica – Parte 5
César Cassiolato, Diretor de Marketing, Qualidade e Assistência Técnica da SMAR Equipamentos Industriais Ltda e Ana Cecília Della Torre, Engenheira Eletricista da SMAR Equipamentos Industriais Ltda.
Introdução
É notório o crescimento do Profibus em nível mundial e, principalmente, no Brasil. Decidimos escrever este artigo, detalhando desde a instalação até a configuração básica, pois temos visto na prática muita instalação de forma inadequada, assim como erros básicos na configuração básica que têm estendido o tempo de comissionamento e startup e, conseqüentemente, gerado uma degradação da qualidade da performance da rede. Dividimos este artigo, pela sua extensão e abrangência em seis partes. Esta é a quinta parte.
Profibus
O PROFIBUS é um padrão de rede de campo aberto e independente de fornecedores, onde a interface entre eles permite uma ampla aplicação em processos e manufatura. Esse padrão é garantido segundo as normas EN 50170 e EN 50254, além da IEC 611158-2 no caso do PROFIBUS PA.
O PROFIBUS DP é a solução de alta velocidade (high-speed) do PROFIBUS. Seu desenvolvimento foi otimizado especialmente para comunicações entre os sistemas de automação e equipamentos descentralizados, voltada para sistemas de controle, onde se destaca o acesso aos dispositivos de I/O distribuídos.
O PROFIBUS DP utiliza a RS485 como meio físico, ou a fibra ótica em ambientes com susceptibilidade a ruídos ou que necessitem de cobertura a grandes distâncias.
O PROFIBUS PA é a solução PROFIBUS que atende aos requisitos da automação de processos, onde se tem a conexão em processos com equipamentos de campo, tais como: transmissores de pressão, temperatura, conversores, posicionadores, etc. Esta rede pode ser usada em substituição ao padrão 4 a 20 mA.
Existem vantagens potenciais da utilização dessa tecnologia, onde resumidamente destacam-se as vantagens funcionais (transmissão de informações confiáveis, tratamento de status das variáveis, sistema de segurança em caso de falha, equipamentos com capacidades de autodiagnose, rangeabilidade dos equipamentos, alta resolução nas medições, integração com controle discreto em alta velocidade, aplicações em qualquer segmento, etc.). Além dos benefícios econômicos pertinentes às instalações (redução de até 40% em alguns casos em relação aos sistemas convencionais), custos de manutenção (redução de até 25% em alguns casos em relação aos sistemas convencionais) e menor tempo de start-up, oferece um aumento significativo em funcionalidade, disponibilidade e segurança.
O PROFIBUS PA permite a medição e controle por um barramento a dois fios. Também permite alimentar os equipamentos de campo e aplicações em áreas intrinsecamente seguras, bem como a manutenção e a conexão/desconexão de equipamentos até mesmo durante a operação, sem interferir em outras estações em áreas potencialmente explosivas. O PROFIBUS PA foi desenvolvido em cooperação com os usuários da Indústria de Controle e Processo (NAMUR), satisfazendo as exigências especiais dessa área de aplicação:
- O perfil original da aplicação para a automação do processo e interoperabilidade dos equipamentos de campo dos diferentes fabricantes;
- Adição e remoção de estações de barramentos mesmo em áreas intrinsecamente seguras sem influência para outras estações;
- Uma comunicação transparente através dos acopladores do segmento entre o barramento de automação do processo (PROFIBUS PA) e do barramento de automação industrial (PROFIBUS-DP);
- Alimentação e transmissão de dados sobre o mesmo par de fios baseado na tecnologia IEC 61158-2;
- Uso em áreas potencialmente explosivas, intrinsecamente segura.
A conexão dos transmissores, conversores e posicionadores em uma rede PROFIBUS DP é feita por um coupler DP/PA. O par trançado a dois fios é utilizado na alimentação e na comunicação de dados para cada equipamento, facilitando a instalação e resultando em baixo custo de hardware, menor tempo para start-up, manutenção livre de problemas, baixo custo do software de engenharia e alta confiança na operação.
O protocolo de comunicação PROFIBUS PA utiliza o mesmo protocolo de comunicação PROFIBUS DP, onde o serviço de comunicação e telegramas são idênticos. Na verdade, o PROFIBUS PA = PROFIBUS DP - protocolo de comunicação + serviços acíclico estendido + IEC 61158, também conhecida como nível H1.
O Profibus permite uma integração uniforme e completa entre todos os níveis da automação e as diversas áreas de uma planta. Isto significa que a integração de todas as áreas da planta pode ser realizada com um protocolo de comunicação que usa diferentes variações.
No nível de campo, a periferia distribuída, tais como: módulos de E/S, transdutores, acionamentos (drives), válvulas e painéis de operação, trabalham em sistemas de automação, através de um eficiente sistema de comunicação em tempo real, o PROFIBUS DP ou PA. A transmissão de dados do processo é efetuada ciclicamente, enquanto alarmes, parâmetros e diagnósticos são transmitidos somente quando necessário, de maneira acíclica.
Este artigo apresenta detalhes de instalações em PROFIBUS-DP e PROFIBUS-PA.
Sempre que possível, consulte a EN50170 e a IEC60079-14 para as regulamentações físicas, assim como para as práticas de segurança em instalações elétricas em atmosferas explosivas.
É necessário agir com segurança nas medições, evitando contatos com terminais e fiação, pois a alta tensão pode estar presente e causar choque elétrico. Lembre-se que cada planta e sistema tem seus detalhes de segurança. Informar-se deles antes de iniciar o trabalho é muito importante.
Para minimizar o risco de problemas potenciais relacionados à segurança, é preciso seguir as normas de segurança e de áreas classificadas locais aplicáveis que regulam a instalação e operação dos equipamentos. Estas normas variam de área para área e estão em constante atualização. É responsabilidade de o usuário determinar quais normas devem ser seguidas em suas aplicações e garantir que a instalação de cada equipamento esteja de acordo com as mesmas.
Uma instalação inadequada ou o uso de um equipamento em aplicações não recomendadas podem prejudicar a performance de um sistema e conseqüentemente a do processo, além de representar uma fonte de perigo e acidentes. Devido a isto, recomenda-se utilizar somente profissionais treinados e qualificados para instalação, operação e manutenção.
Dando continuidade à quinta parte, temos:
Endereçamento Utilizando Couplers DP/PA
A Figura 1.1 apresenta em detalhes o endereçamento transparente quando são utilizados couplers (de baixa ou de alta velocidade) na rede PROFIBUS DP e PROFIBUS PA. O endereço default é 126 e somente um equipamento com 126 pode estar presente no barramento de cada vez.
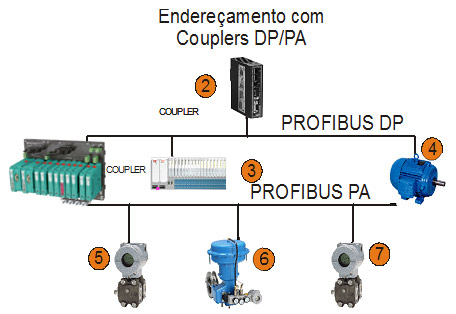
Figura 1.1 – Endereçamento Transparente com a Utilização de Coupler DP/PA.
Já a Figura 1.2 mostra em detalhes o endereçamento estendido quando se utiliza o link DP/PA na rede PROFIBUS DP e PROFIBUS PA.
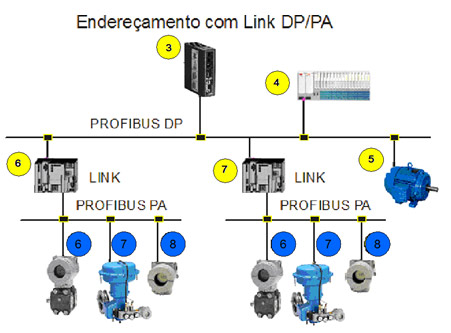
Figura 1.2 – Endereçamento estendido com a utilização de link DP/PA.
Os endereços de 3 a 5 não são utilizados para endereças links.
Shield e Aterramento
Ao considerar a questão de shield e aterramento em barramentos de campo, deve-se levar em conta:
- A compatibilidade eletromagnética (EMC).
- Proteção contra explosão.
- Proteção de pessoas.
De acordo com a IEC61158-2, aterrar significa estar permanentemente conectado ao terra através de uma impedância suficientemente baixa e com capacidade de condução suficiente para prevenir qualquer tensão que possa resultar em danos de equipamentos ou pessoas. Linhas de tensão com 0 Volts devem ser conectadas ao terra e serem galvanicamente isoladas do barramento fieldbus. O propósito de se aterrar o shield é evitar ruídos de alta freqüência.
Preferencialmente, o shield deve ser aterrado em dois pontos, no início e final de barramento, desde que não haja diferença de potencial entre estes pontos, permitindo a existência e caminhos a corrente de loop. Na prática, quando esta diferença existe, recomenda-se aterrar shield somente em um ponto, ou seja, na fonte de alimentação ou na barreira de segurança intrínseca. Deve-se assegurar a continuidade da blindagem do cabo em mais do que 90% do comprimento total do cabo.
O shield deve cobrir completamente os circuitos elétricos através dos conectores, acopladores, splices e caixas de distribuição e junção.
Nunca se deve utilizar o shield como condutor de sinal. É preciso verificar a continuidade do shield até o último equipamento PA do segmento, analisando a conexão e acabamento, pois este não deve ser aterrado nas carcaças dos equipamentos.
Em áreas classificadas, se uma equalização de potencial entre a área segura e área perigosa não for possível, o shield deve ser conectado diretamente ao terra (Equipotencial Bonding System) somente no lado da área perigosa. Na área segura, o shield deve ser conectado através de um acoplamento capacitivo (capacitor preferencialmente cerâmico (dielétrico sólido), C<= 10nF, tensão de isolação >= 1.5kV).
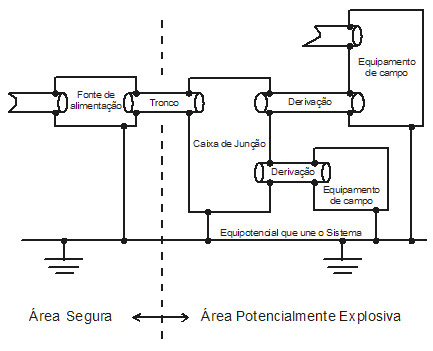
Figura 1.3 – Combinação Ideal de Shield e Aterramento.
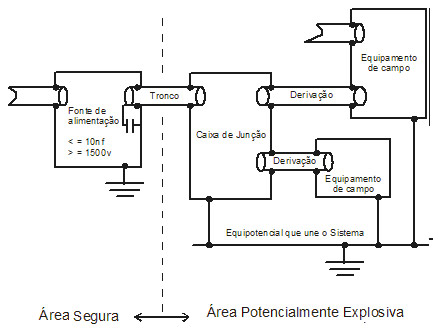
Figura 1.4 – Aterramento Capacitivo.
A IEC61158-2 recomenda que se tenha a isolação completa. Este método é usado principalmente nos Estados Unidos e na Inglaterra. Neste caso, o shield é isolado de todos os terras, a não ser o ponto de terra do negativo da fonte ou da barreira de segurança intrínseca do lado seguro.O shield tem continuidade desde a saída do coupler DP/PA, passa pelas caixas de junções e distribuições e chega até os equipamentos. As carcaças dos equipamentos são aterradas individualmente do lado não seguro. Este método tem a desvantagem de não proteger os sinais totalmente dos sinais de alta freqüência e, dependendo da topologia e comprimento dos cabos, pode gerar em alguns casos a intermitência de comunicação. Recomenda-se nestes casos o uso de canaletas metálicas.
Uma outra forma complementar à primeira, seria ainda aterrar as caixas de junções e as carcaças dos equipamentos em uma linha de equipotencial de terra, do lado não seguro. Os terras do lado não seguro com o lado seguro são separados.
A condição de aterramento múltiplo também é comum, onde se tem uma proteção mais efetiva às condições de alta freqüência e ruídos eletromagnéticos. Este método é preferencialmente adotado na Alemanha e em alguns países da Europa. Neste método, o shield é aterrado no ponto de terra do negativo da fonte ou da barreira de segurança intrínseca do lado seguro e além disso, no terra das caixas de junções e nas carcaças dos equipamentos, sendo estas também aterradas pontualmente, no lado não seguro. Uma outra condição seria complementar a esta, porém os terras seriam aterrados em conjunto em uma linha equipotencial de terra, unindo o lado não seguro ao lado seguro.
Para mais detalhes, sempre consultar as normas de segurança do local. Recomenda-se utilizar a IEC60079-14 como referência em aplicações em áreas classificadas.
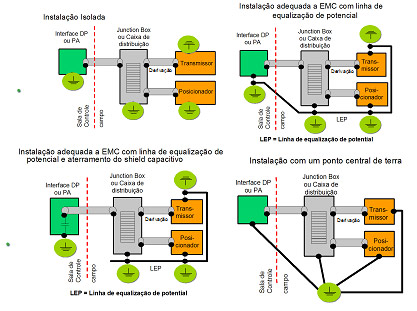
Figura 1.5 – Várias Formas de Aterramento e Shield.
Número de Equipamentos PROFIBUS PA em um Segmento
A quantidade de equipamentos (N) por segmento PA é função do consumo quiescente de cada equipamento PA, das distâncias envolvidas (resistência de loop cabo tipo A: 44 Ω/km), do coupler DP/PA e de sua corrente drenada, da classificação de área (couplers para área classificada drenam correntes da ordem de 110 mA, tensão de saída 12 V), além da corrente de FDE (normalmente 0mA, dependendo do fabricante). A corrente total no segmento deve ser menor do que a drenada pelo coupler. Equipamentos SMAR consomem 12 mA.
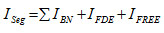
Sendo que:
Onde:
Corrente no segmento PA;
Somatória das correntes quiescentes de todos os equipamentos no segmento PA;
Corrente adicional em caso de falha, normalmente desprezível;
Corrente de folga, útil em caso de expansão ou troca de fabricante, recomendado 20 mA;
Corrente drenada pelo coupler.
Além disso, deve-se ter pelo menos 9.0 V na borneira do equipamento PA mais distante do coupler DP/PA para garantir a energização correta do mesmo:
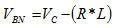
Onde:
Tensão de saída do coupler DP/PA;
Resistência de Loop (Cabo tipo A, R = 44 Ω/km);
Comprimento total do barramento PA;
Tensão na borneira do equipamento PA mais distante do coupler DP/PA.
Sendo . Isto garante a energização do último equipamento PA. Lembrando que o sinal de comunicação deve ter excursão de 750 a 1000 mV.
Algumas caixas de junções ou protetores de curto para segmento, chamados spur guards são ativos e podem ser alimentados via barramento PA (H1), sendo assim, deverá entrar no cálculo da somatória da corrente. Além disso, cada saída destes spur guards possui um limite permitido de corrente que deve ser respeitado.
Arquivos GSDs (Device Database Files)
O Profibus requer um arquivo conhecido como GSD que descreve o equipamento e tem em detalhes os dados de entrada e saída, seus formatos (indentifier numbers), taxas de comunicação suportadas, se possui ou não o comando de mudança de endereço (Address Change), versão de hardware e firmware, etc. Estas informações são utilizadas pelo mestre Profibus durante a troca de dados cíclicos. Normalmente existem arquivos bmp associados a cada equipamento. Os arquivos dos equipamentos SMAR estão disponíveis em:
http://www.smar.com/files/DevicesLibrary/SMAR_DeviceLibrary_Version1_11%20-20Profibus.zip
Existem três tipos de profiles para equipamentos PROFIBUS PA de acordo com a versão dos arquivos GSD:
- Manufacuter Specific: Este tipo garante o máximo de funcionalidade, de acordo com o fabricante;
- Profile Specific: Este tipo contém um número fixo de AI (Analog Input) block e se o equipamento é trocado por um outro de fabricante diferente, este novo equipamento terá as mesmas características padrões;
- Profile Multi-variable: O equipamento terá como ID number o número 0x9760 e o arquivo GSD conterá todos os blocos especificados no perfil do equipamento, tais como, AI, DO, DI, etc.
Na grande maioria dos casos, os equipamentos são usados como o GSD de acordo com o tipo Manufacuter Specific, onde se garante o máximo de funcionalidade, de acordo com o fabricante.
Dependo do sistema PROFIBUS utilizado, este possui um diretório onde os arquivos GSDs devem ser copiados e um outro específico para cópia dos arquivos bmps. Alguns sistemas, após a cópia necessitam que se dê um comando de scan GSD, para atualizar a ferramenta de configuração cíclica.
Exemplos de Dados Cíclicos
Os blocos de funções de entrada e saída podem ser configurados para trocas de dados cíclicos, como um link entre dois parâmetros em equipamentos diferentes. A troca de dados cíclica indica que um parâmetro de entrada de um bloco de função obtém seu valor do parâmetro de saída específico de outro bloco de função em outro equipamento ciclicamente.
Em geral, um bloco de função do transmissor ou o atuador faz a troca de dados cíclicos com o equipamento controlador Mestre (por exemplo, o DF73 ou um PLC). Normalmente o transmissor obtém os dados do sensor e o equipamento controlador recebe estes dados e realiza um cálculo e envia uma informação ao atuador, que os recebe e faz algumas ações no processo de acordo com uma estratégia de controle.
Os equipamentos SMAR têm a seguinte definição de módulos e blocos:
- LD303 | Transmissor de Pressão PROFIBUS - O arquivo GSD (smar0895.gsd) define 2 módulos para este equipamento: O primeiro para a Entrada Analógica e o segundo para o Totalizador. Isto significa que o LD303 tem dois Blocos de Função principais disponíveis, o Bloco de Entrada Analógico e o Bloco Totalizador, respectivamente nesta ordem. Assim, a configuração da leitura cíclica quando não utiliza o Totalizador deve ser a seguinte: Entrada Analógica (0x94) e módulo vazio (0x00), respectivamente. Porém, se utilizar o Totalizador, o LD303 ainda requisitará dois módulos: Entrada Analógica (0x94) e Totalizador (0x41,0x84, 10x85), respectivamente;
- TP303 | Transmissor de Posição PROFIBUS - O arquivo GSD (smar0904.gsd) define 2 módulos para este equipamento: 1 para a Entrada Analógica e 1 para o Totalizador;
- TT303 | Transmissor de Temperatura PROFIBUS - O arquivo GSD (smar089A.gsd) define dois módulos para este equipamento: Eles têm dois módulos para o Bloco de Entrada Analógica. Isto significa que o TT303 tem dois blocos de Entrada Analógica. Normalmente, é necessário usar só um bloco AI para a medida da temperatura. No caso de ter dois sensores diferentes, os dois blocos de Entrada Analógica devem ser usados. Conseqüentemente, têm-se duas medidas de temperatura independentes, uma por canal.
O manual específico para o TT303 descreve a configuração dos parâmetros necessários e mostra o diagrama de conexão para os diferentes tipos de sensores (este diagrama está mencionado no documento acima). Os únicos casos onde os dois blocos de Entrada Analógicos devem ser usados são os dois últimos neste diagrama. Se configurar apenas um sensor é necessário configurar os dois módulos, um para a Entrada Analógica 1 (0x94) e outro para o módulo vazio (0x00), respectivamente. Porém, se o TT303 foi configurado para duas medidas independentes, dois módulos devem ser configurados, um para a Entrada Analógica 1 e outro para a Entrada Analógica 2.
Assim, é muito importante saber que sempre que estiver usando só um sensor, sempre haverá necessidade de configurar dois módulos para a leitura cíclica pelo Mestre DP.
- IF303 | Conversor de Corrente PROFIBUS - O arquivo GSD (smar0896.gsd) define 6 módulos para este equipamento: 3 módulos para a Entrada Analógica e 3 para o Totalizador (um AI e um bloco de função TOT para cada terminal);
- FY303 | Posicionador de Válvulas PROFIBUS - O arquivo GSD (smar0897 .gsd) define 1 módulo para este equipamento: 1 módulo para a Saída Analógica;
- FP303 | Conversor de Pressão PROFIBUS - O arquivo GSD (smar0898 .gsd) define 1 módulo para este equipamento: 1 módulo para a Saída Analógica;
- FI303 | Conversor de Corrente PROFIBUS - O arquivo GSD (smar0899.gsd) define 3 módulos para este equipamento: 3 módulos para a Saída Analógica (Um bloco AO para cada terminal);
- LD293 | Transmissor de Pressão PROFIBUS - O arquivo GSD (smar0906.gsd) define 1 módulo para este equipamento: o módulo para o bloco de Entrada Analógica;
- DT303 | Transmissor de Desnsidade PROFIBUS - O arquivo GSD (smar0905.gsd) define 1 módulo para este equipamento: o módulo para o bloco de Entrada Analógica, para versões de firmware menores que 2.00. Para versões maiores ou iguais a 2.00, o DT303 utiliza o arquivo GSD (smar0905a.gsd) que define 3 módulos de Entrada Analógica para este equipamento, nesta ordem: concentração, densidade (Kg/m3) e temperatura.
De acordo com a Tabela 1.1 têm-se os blocos de função disponíveis, a ordem em dados cíclicos, o número de módulos necessários e o endereço defaultpara cada equipamento da SMAR.
Nesta mesma Tabela é possível observar a definição da ordem do buffer para leitura de dados cíclicos, onde esta ordem é descrita com mais detalhes.
* Versão de Firmware
Equipamento |
Bloco Funcional Disponível |
Ordem na Troca de Dados Cíclicos |
Números de Módulos |
Endereço Default |
AI |
AO |
TOT |
1 |
2 |
3 |
4 |
5 |
6 |
LD303 |
1 |
- |
1 |
AI |
TOT |
- |
- |
- |
- |
2 |
126 |
TP303 |
1 |
- |
1 |
AI |
TOT |
- |
- |
- |
- |
2 |
126 |
TT303 |
2 |
- |
- |
AI |
AI |
- |
- |
- |
- |
2 |
126 |
IF303 |
3 |
- |
3 |
AI |
AI |
AI |
TOT |
TOT |
TOT |
6 |
126 |
FY303 |
- |
1 |
- |
AO |
- |
- |
- |
- |
- |
1 |
126 |
FP303 |
- |
1 |
- |
AO |
- |
- |
- |
- |
- |
1 |
126 |
FI303 |
- |
3 |
- |
AO |
AO |
AO |
- |
- |
- |
3 |
126 |
LD293*
DT303
<2.00 |
1 |
- |
- |
AI |
- |
- |
- |
- |
- |
1 |
126 |
DT303*
>=2.00 |
3 |
|
|
AI |
AI |
AI |
|
|
|
3 |
126 |
Tabela 1.1 - Definição da Ordem para Leitura de Dados Cíclicos
FB |
Parâmetro |
Identifier Byte |
Formato Identifier Estendido |
AI |
OUT |
0x94 |
0x42,0x84,0x08,0x05 |
AO |
SP |
0xA4 |
0x82,0x84,0x08,0x05 |
SP/READBACK/POS_D |
0x96,0xA4 |
0xC6,0x84,0x86,0x08,0x05,0x08,0x05,0x05,5x05 |
SP/CHECK_BACK |
0x92,0xA4 |
0xC3,0x84,0x82,0x08,0x05,0x0A |
SP/READBACK/POS_D/CHECK_BACK |
0x99,0xA4 |
0xC7,0x84,0x89,0x08,0x05,0x08,0x05,0x05,0x05,0x0A |
RCAS_IN/RCAS_OUT |
0xB4 |
0xC4x84,0x84,0x08,0x05,0x08,0x05 |
RCAS_IN/RCAS_OUT/CHECK_BACK |
0x97,0xA4 |
0xC5,0x84,0x87,0x08,0x05,0x08,0x05,0x0A |
SP/READBACK/ RCAS_IN/RCAS_OUT/ POS_D/CHECK_BACK |
0x9E,0xA9 |
0xCB, 0x89, 0x8E, 0x08, 0x05, 0x08, 0x05, 0x08, 0x05, 0x08, 0x05, 0x05, 0x05, 0x0A |
TOT |
TOTAL |
- |
0x41,0x84,0x85 |
TOTAL/SETTOT |
- |
0xC1,0x80,0x84,0x85 |
|
TOTAL/SETTOT/MODETOT |
- |
0xC1,0x81,0x84,0x84 |
Tabela 1.2 - Indentifier Numbers de Acordo com os Blocos Funcionais e definidos nos Arquivos Gsds.
Formato Float IEEE 754
O formato float usado no PROFIBUS está definido de acordo com o IEEE:
byte_MSB(byte1) byte2 byte3 byte_LSB (byte4)
byte_MSB(byte1) = exp
byte2 = mantissa
byte3 = mantissa
byte_LSB(byte4) = mantissa
Exemplo: 41 F1 01 80 => 30.1255
01000001 11110001 00000001 1000000
float = (-1)^bitsignal*[2^(exp-127)*[1+mantissa]]
onde:
bit signal é o bit msb bit do byte_MSB(byte1),
Se este bit é 0, o número é positivo e se for 1, é negativo.
No exemplo, o número é positivo.
exp é a soma dos outros bits do byte_MSB(byte1) e do bit msb do byte2.
No exemplo:
1*2^7+0*2^6+0*2^5+0*2^4+0*2^3+0*2^2+1*2^1+1*2^0 = 2^7+2^1+2^0
mantissa: segue a mesma regra do exp desde o byte2 até o byte_LSB(byte4), até o fator exponencial –23:
1*2^(-1)+1*2^(-2)+1*2^(-3)+1*2^(-7)+1*2^(-15)+1*2^(-10)
Então, float = (1)*[2^(129-127)]*1.8828125 = 30.1255
Status Code
Segundo o profile V 3.0, as variáveis de status seguem a tabela a seguir, onde:
- De 0x00 a 0x3F => Device Status: Bad;
- De 0x40 a 0x7F => Device Status: Uncertain;
- 0x80 => Device Status: Good
|
Qualidade |
Sub-status |
Limites |
Bom
(NC) |
A qualidade do valor é boa.
Possíveis condições de alarme podem ser indicadas pelo sub-status. A indicação do alarme só é planejada para PV e não para saída. |
Não Especificado |
Não Limitado:
O valor está dentro dos limites.
Limite Baixo:
O valor está abaixo do limite.
Limite Alto:
O valor está acima do limite alto.
Constantes:
OS limites baixos e altos são os mesmos, fazendo o valor constante. |
Bloco Alarme |
Alarme Auxiliar Ativo |
Alarme Critico Ativo |
Block Alarm não reconhecido |
Alarme consultivo não reconhecido |
Alarme Critico Alarm não reconhecido |
Bom
(cascata) |
O valor deve ser usado em controle. |
Não-especificado |
Inicialização Reconhecida |
Pedido de Inicialização |
Não Convidado |
Não Selecionado |
Não Selecionado |
Local Override |
Falha Segura Ativa |
Falha Segura Inciada |
Incerto |
A qualidade do valor é menor que a normal, mas o valor pode ainda ser útil. |
Não-especificado |
Último Valor Utilizado |
Substituto |
Valor Inicial |
Conversão do sSensor Não-Precisa |
Violação da Faixa em Unidades de Engenharia |
Subnormal |
Fora de Serviço |
Ruim |
O valor não é utilizado. |
Não-especificado |
Erro de Configuração |
Não Conectado |
Dispositivo com danos |
Sensor com danos |
Sem comunicação...com último valor utilizado |
Sem comunicação...com último valor utilizado |
Fora de Serviço |
Tabela 1.4 – Status Code
Conclusão
Vimos neste artigo vários detalhes importantes. Veremos mais detalhes na última parte do artigo na próxima edição.
Vale a pena lembrar que o sucesso de toda rede de comunicação está intimamente ligada à qualidade das instalações.
Sempre consulte as normas.
O seu tempo de comissionamento, start-up e seus resultados podem estar comprometidos com a qualidade dos serviços de instalações.
Como cliente, contrate serviços de empresas que conheçam e dominam a tecnologia Profibus e que façam instalações profissionais e de acordo com o padrão Profibus.
Referências
- Manuais SMAR Profibus
- www.smar.com.br
- Material de Treinamento em Profibus - César Cassiolato
- Especificações técnicas Profibus.
|